Нефтедобывающая промышленность не отстает от других сфер экономики по внедрению IoT и искусственного интеллекта на свои производства. Это позволяет сэкономить средства на сотрудниках, оптимизировав их количество, предотвратить поломку важного узла и сократить выбросы. Последнее звучит актуально в условиях повышенного внимания к добывающим секторам экономики на фоне обострившейся дискуссии о глобальных изменениях климата. «Хайтек» поговорил на IoT World Summit 2018 с главным инженером малайзийской нефтегазовой компании Petronas Шарулем Рашидом о концепции мобильного работника, применении ИИ на заводах и доверии стейкхолдеров.
Petronas — мировая нефтегазовая компания. С момента основания в 1974 году имеет деловые интересы в 35 странах мира. Полностью принадлежит правительству Малайзии. Наделена полномочиями добычи всей нефти и газа в Малайзии. На корпорацию возложены обязанности разработки и добавления стоимости таких ресурсов. Petronas занял 191 место в списке Fortune Global 500 крупнейших корпораций в мире. Также концерн Petronas занимает 12 место среди самых прибыльных компаний в мире и является самой прибыльной в Азии.
Концепция мобильного сотрудника
— Когда вы начали внедрять IoT технологии в Petronas?
— В нефтеперерабатывающих предприятиях цифровые технологии существуют уже довольно давно. ПЛК (программируемый логический контроллер — «Хайтек»), РСУ (распределенные системы управления — «Хайтек») — это все тоже цифровые технологии. Разные сенсоры, измеряющие, к примеру, давление — они существовали до нас. Наша задача сейчас — сфокусироваться и приложить усилия к тому, чтобы улучшить свои системы. Там, где мы видим проблемы, ИТ-команда приходит с нужным программным обеспечением — например, для предсказаний. С помощью поступающих данных можно построить систему раннего оповещения и улучшить заводы, следовательно, быть более конкурентоспособными.
— Сейчас вы в основном используете IoT-технологии для предсказаний на основе собранных данных?
— Есть две части. Первая — автоматизация повторяемых задач и процессов. Когда оператор проверяет оборудование, он занимается рутинной работой и записывает все данные в свой блокнот. Эти данные могут быть потеряны. Мы предоставляем им цифровую платформу, чтобы использовать портативные компьютеры для внесения данных. Все эти данные сразу переносятся в централизованную базу. Так информация не теряется, дальше ее можно анализировать. Технические специалисты пишут отчеты на портативных устройствах, инженеры анализируют информацию, занимаются необходимыми исправлениями. Так мы уменьшаем долю рутинной работы и увеличиваем эффективность заводов.
Вся информация о запасных деталях, все проблемы — это есть в портативных устройствах. Сотрудники могут запросить необходимые детали по их номеру с телефона. И ремонт будет крайне быстрым. Там можно найти даже необходимые инструкции по процедурам ремонта. Мы называем это мобильным сотрудником.
Мы также занимаемся предиктивным техобслуживанием. Некоторое оборудование может отказать, и ничего критического в этом не будет. Его просто чинят, так как оно не влияет на работу всего завода. Но с критически важным оборудованием так делать нельзя, нужна стратегия. Определенное оборудование необходимо отключать после 8 тыс. часов работы и проводить инспекцию. Но используя предиктивную аналитику, мы можем следить за состоянием оборудования и продлить время его работы на какое-то количество часов. Так можно сэкономить много денег.
«У компаний, у которых нет IoT, нет и данных»
— Сколько у вас заводов по всему миру?
— Трудно вспомнить конкретную цифру, от 30 до 50.
— Заводы отличаются друг от друга в плане используемых технологий?
— Некоторые заводы далеко впереди, некоторые сильно отстают. Мы ищем лучшие практики и переносим их на старые заводы. Сейчас у нас есть единая цифровая стратегия. Есть руководители цифровой стратегии из ИТ и IoT — вместе они находят решения, которые позволят вывести компанию на новый уровень. На основе этой стратегии головной офис будет двигаться к единству цифровых систем.
— Есть ли у вас единая система для всех данных?
— Сейчас у нас есть единая цифровая PI система OSIsoft. Это платформа, в которую загружаются все данные с DCS (распределенные системы управления — «Хайтек»). К сожалению, у нас нет единого стандарта DCS. Один завод может использовать систему Honeywell, второй — Yokogawa, третий — Foxboro. Их очень много. Но данные разных DCS поступают в единую платформу. С этими данными уже можно делать все, что угодно — предсказания, добавление искусственного интеллекта.
— Вы используете ИИ и машинное обучение?
— Да. Например, используем ИИ в наших закупках. С его помощью мы анализируем имеющийся инвентарь на складах, это позволяет оптимизировать хранение. Потому что склады — это много денег. Но на основе данных можно сказать, что именно нам надо хранить, а что не надо, и в каком количестве. Если кто-то говорит, что нужно хранить запасные части для страховки, мы показываем данные.
Данные — это инструмент, который позволяет стейкхолдерам лучше распоряжаться деньгами. У тех заводов, у которых нет данных, нет возможности убедить стейкхолдеров потратить деньги в нужное время на нужные вещи, когда это необходимо. У компаний, у которых нет IoT, нет и данных. Если у вас нет данных, как вы убедите стейкхолдеров?
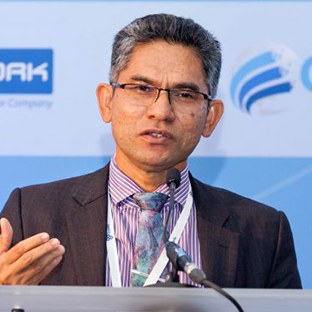
Шаруль Рашид
Например, для нового завода мы объединили усилия с саудовской компанией Aramco. Это проект в Пенгеранге, Малайзия. Производство — 300 тыс. баррелей в день. Нам нужно предоставить им данные, чтобы они увидели эффективность. Если бы я был стейкхолдером, то бы не доверял людям, нужна некоторая дистанция. Мне было бы нужно посмотреть на данные и из них понять, что на самом деле происходит на заводе. Мне нужно, чтобы была безопасность, эффективность, — и чтобы эти значения были основаны на данных.
«Если работа не требует людей, мы их убираем»
— У вас есть заводы по всему миру. Везде ли одинаково просто внедрять новые технологии?
— Нужно понимать местную культуру, а значит, делать это таким способом, чтобы всем было комфортно. Конечно, в Южной Африке, к примеру, это труднее. В Малайзии проще.
— Сколько в среднем сенсоров задействовано на одном заводе?
— Количество сенсоров зависит от размера завода. На большом заводе может быть 50 тыс. устройств, на маленьком — 10 тыс.
— Какие основные функции сенсоров?
— Они нужны для контроля и мониторинга. Сенсоры измеряют все — давление, уровни, температуру, поток. Все эти параметры не должны превышать определенных пределов.
— Внедрение такого количества сенсоров — это довольно дорого. Как быстро окупаются затраты?
— Когда мы хотим что-то внедрить, то проводим расчеты по окупаемости на каждом проекте. Обычно это занимает один или два года. Да, это дорого, но беспроводная связь дала нам возможность сильно снизить затраты. Прокладывать кабели очень дорого, а сегодня мы можем использовать беспроводные детекторы газа.
— Если говорить об экологии, данные как-то позволяют снизить выбросы?
— По вопросам экологии работаем вместе с Департаментом окружающей среды Малайзии. Мы установили сенсоры, которые фиксируют выбросы. Так как Малайзия запустила акт о возобновляемой энергии, нам нужно соответствовать его требованиям.
— Можно ли стремиться к чистой энергии, работая в нефтегазовой промышленности?
— Нужно постараться найти баланс. Я не могу комментировать больше это.
— Каким будет будущее индустрии? Останутся ли вообще на заводах люди?
— Люди необходимы. Но количество людей можно оптимизировать. Petronas пересматривает традиционные процессы, и если люди в них необходимы, пусть они остаются. Если работа не требует людей, мы их убираем. Это зависит от конкретного процесса.