В современном горнодобывающем секторе возрастает значимость человеческого фактора как ключевого риска. Эта проблема негативно влияет на производительность предприятий и становится основной причиной нарушений правил безопасности. За 2024 год количество аварий на промышленных предприятиях выросло на 15%. 30% всех эксцессов происходят именно в добыче полезных ископаемых, где число инцидентов по сравнению с 2023 годом увеличилось на 20%. При этом 70% всех аварий происходили из-за человеческого фактора: 40% — нарушения техники безопасности, 30% — ошибки персонала. Лишь 20% случаев связаны с механическими неисправностями оборудования, а 10% — с природными факторами.
Пример успешного решения этих проблем — проект TAPP Group по внедрению искусственного интеллекта на обогатительном предприятии.
Предпосылки проекта
Фабрика столкнулась с типичной для промышленности проблемой — нестабильностью показателей из-за человеческого фактора. Ручная настройка давала кратковременный эффект. Выход полезного ископаемого вырастал на 6,5%, но через 3 дня возвращался к прежним значениям. Каждый сотрудник регулировал оборудование по собственному усмотрению без единого стандарта.
К этому добавлялись и другие сложности: техника быстро изнашивалась, требования безопасности часто противоречили необходимости непрерывного производства, а аварийные остановки приводили к миллионным убыткам. Перегрузы, отсутствие своевременного ремонта и анализа состояния ухудшали ситуацию.
Недостаток точных регулировок щелей дробилок в процессе работы вызывали закрупнение материала и снижение уровня измельчения в мельницах. План производства срывался. Расчеты провели, оборудование перестроили, но проблема человеческого фактора оставалась.
Специалисты определили необходимость системы с единым алгоритмом работы. Она должна круглосуточно отслеживать крупность материала и автоматически регулировать участок дробления при отклонениях. Фабрика нуждалась в переходе от реактивного к проактивному управлению. Поэтому руководство обратилось к TAPP Group для внедрения комплекса решений на базе ИИ.
Этапы реализации
Команда TAPP Group начала работы с участка дробления руды. Этот выбор не случаен: здесь ручная настройка давала прирост производительности до 6,5%, а внедрение ИИ обещало максимальный экономический эффект.
Задача системы — дробить руду до размера 0-30 мм, не допуская кусков крупнее 30 мм. Для этого установили камеры высокого разрешения над конвейером. За 3 месяца тестового режима собрали базу фотографий для обучения нейросети.
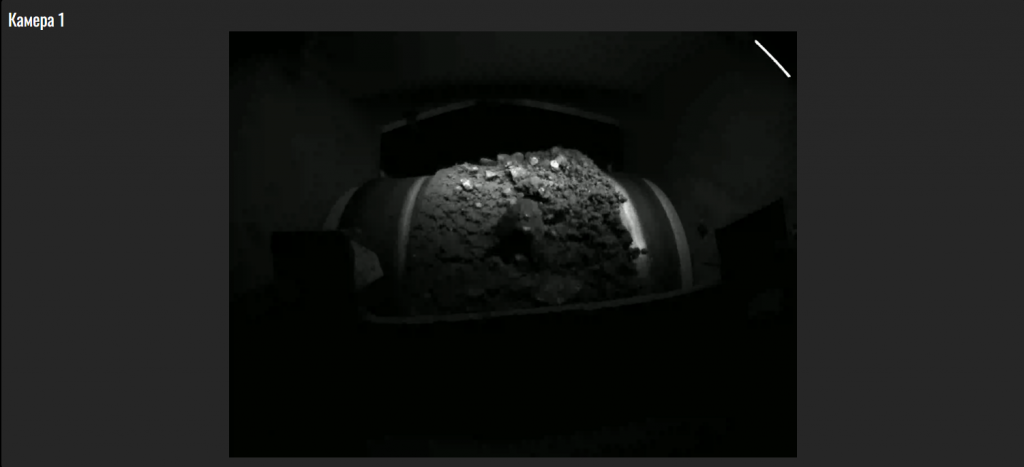
Эксперты провели анализ проб и научили систему определять размеры фракций визуально, без специальных датчиков. Однако возникло и техническое препятствие: немецкие дробилки блокировали внешнее управление. Инженеры TAPP Group изучили алгоритм работы, переписали программу и заменили оригинальные контроллеры на собственные.
Система объединяет данные с камер, датчиков и корпоративных информационных систем (SCADA, MES, ERP) и уже превосходит требования заказчика. Она анализирует ситовый состав материала, определяет соотношение разных фракций и отображает данные на мониторе оператора в реальном времени.
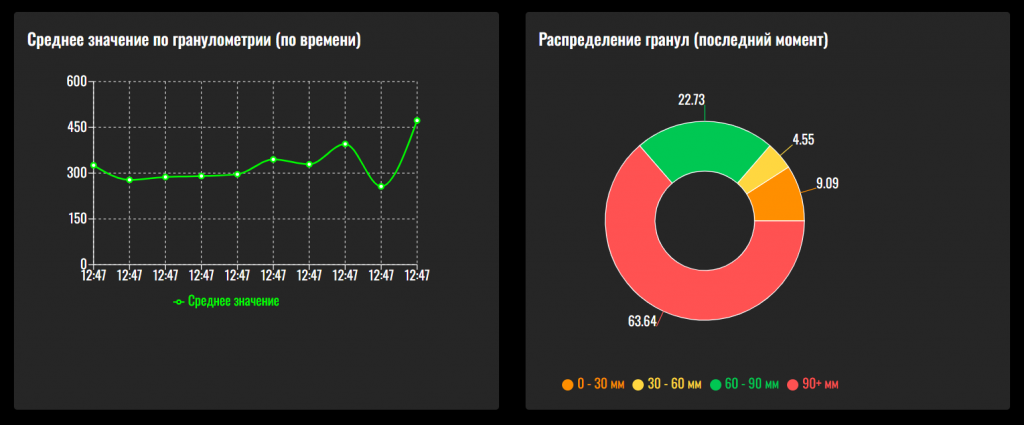
Полный технологический процесс на фабрике включает четыре этапа:
- Дробление руды до нужного размера (текущий этап проекта).
- Измельчение в мельнице до класса -1 миллиметр.
- Доведение материала до 0,1 миллиметра и выделение полезного класса 71 микрон.
- Флотация — основной обогатительный процесс.
После оценки результатов первого этапа TAPP Group планирует внедрить систему на остальных участках параллельно: измельчение, гидрциклоны и флотация.
Искусственный интеллект будет анализировать, из какого забоя или пласта привезли руду и как она дробится. В дальнейшем система сможет адаптировать настройки под конкретные характеристики сырья. Например, для мягкой руды — увеличивать нагрузку и оптимизировать другие параметры.
Успешное внедрение ИИ на всех участках приближает фабрику к концепции безлюдного производства. Первый шаг уже сделан, и скоро предприятие получит оценку его экономической эффективности.
Результаты и перспективы
Даже на этапе дробления технология ИИ повысила извлечение полезного ископаемого на 15%, а оптимистичные прогнозы говорят о росте до 22%. Простои оборудования сократятся с 25 до 10% календарного времени в год.
Для сравнения, раньше фабрика достигала лишь 65% выработки извлечения при максимальном напряжении человеческих ресурсов. После полного внедрения этот показатель вырастет до 90–93%.
ИИ выходит за рамки обычной автоматизации. Система учится на новых данных, сама предлагает решения и объясняет оператору логику действий. Это повышает доверие персонала к технологии.
Дальнейшие этапы развития проекта:
- Автоматизация измельчения материала и разделения в гидроциклонах.
- Внедрение ИИ в работу энергомеханической службы для анализа запчастей и прогноза ремонтов.
- Настройка камер для автоматической остановки механизмов при появлении людей в опасных зонах.
- Создание «умного» карьера с дронами и беспилотной техникой.
Инновационный подход к добыче особенно эффективен из-за неравномерности распределения ценных компонентов. В одном забое содержание достигает 14%, в другом — всего 8%. ИИ выберет выгодные участки и создаст усреднительные склады, куда «умные» самосвалы будут свозить руду. В будущем технология позволит создать полностью безлюдный карьер. Это решит проблему нехватки персонала в отдаленных районах.
Экономический эффект складывается из трех факторов: роста выхода продукции на 15%, сокращения штата в три раза и уменьшения простоев на 15%. Проект демонстрирует переход от реактивного к проактивному управлению. Вместо устранения аварий система предсказывает проблемы и предотвращает их. Этот подход повышает безопасность и эффективность, открывая новую эру в горнодобывающей промышленности.
Обложка: downloaded from Freepik